The 1956 C-172 I bought has an old Delco Remy pull starter for its Continental O-300. It sometimes acts up. A search for solutions uncovered a document authored by Ron Wanttaja that helps diagnose and possibly fix problems with such starters. However, I'm leasing the plane to a flying club so I think it best to install a modern pushbutton lightweight starter to make things easier for everyone flying the plane. I believe this starter will work:
bandc.com
But I don't quite understand this part:
"The B&C Starter for Continental engines is STC-PMA approved for use in certificated aircraft, and is available with or without the STC."
So my question is: Under what circumstances, if any, would I need STC paperwork for my aircraft if the part is also available under a PMA? Who would need to install under STC? (It looks like the STC was issued in 1994 and the PMA approved in 2005.)
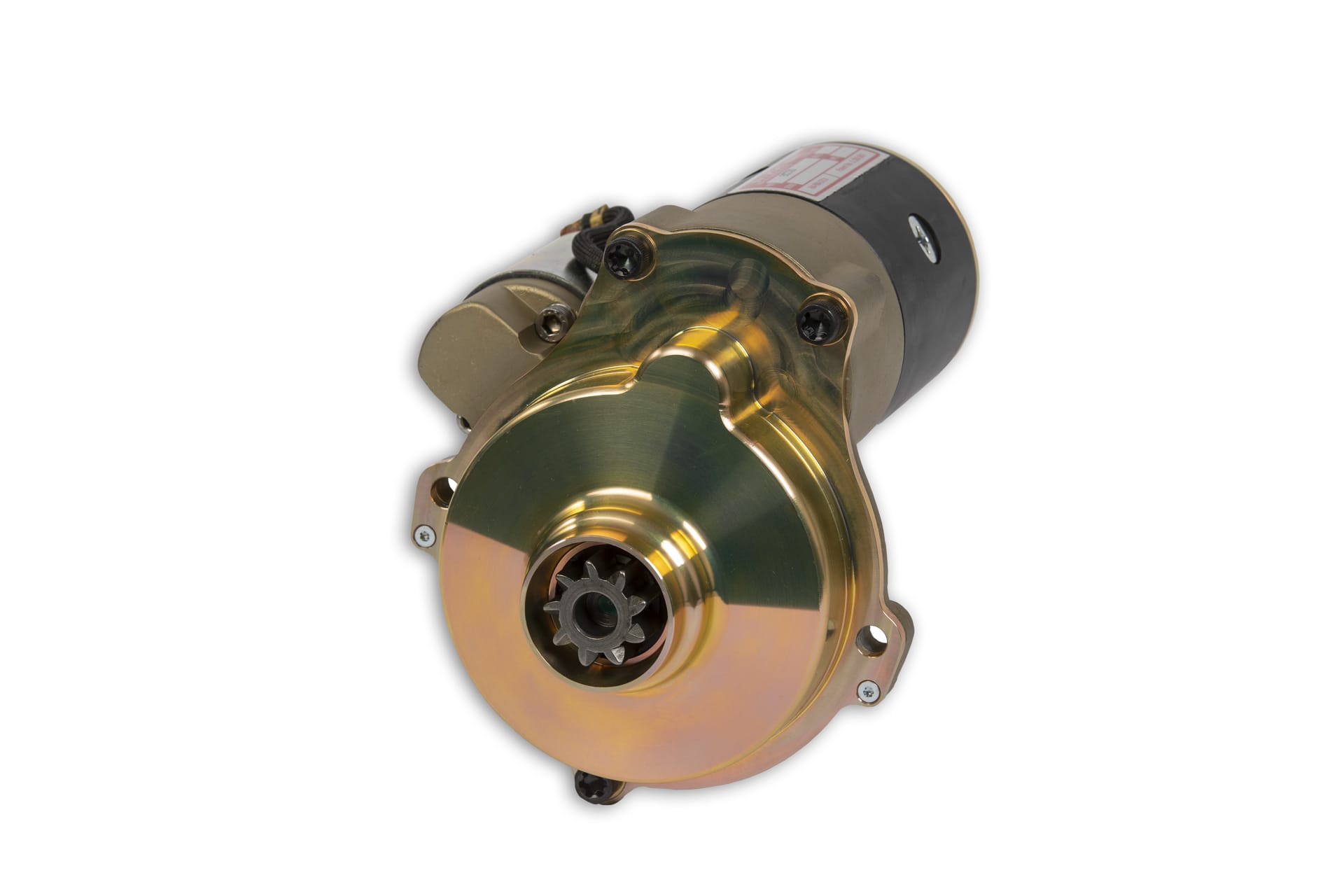
BC320-1 Continental Starter (STC/PMA) - B&C Specialty Products
The B&C Starter for Continental engines (C-75, C-85, C-90, C-145-2, O-200, IO-240, O-300-A, -B, and -C, and GO-300-A, -B, and -C) solves all the problems that other starter designs have had: worn-out clutches, broken pinions, nagging oil leaks, and catastrophic failure modes. Featuring the...
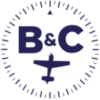
"The B&C Starter for Continental engines is STC-PMA approved for use in certificated aircraft, and is available with or without the STC."
So my question is: Under what circumstances, if any, would I need STC paperwork for my aircraft if the part is also available under a PMA? Who would need to install under STC? (It looks like the STC was issued in 1994 and the PMA approved in 2005.)